Warehouse automation: The key to maximising efficiency at your business.
The global warehouse automation market is expected to grow to $31.03 billion by 2026. It is a market that is growing at speed due to many reasons. Not only can warehouse automation help businesses improve accuracy, compliance and safety — it drives efficiency across teams.
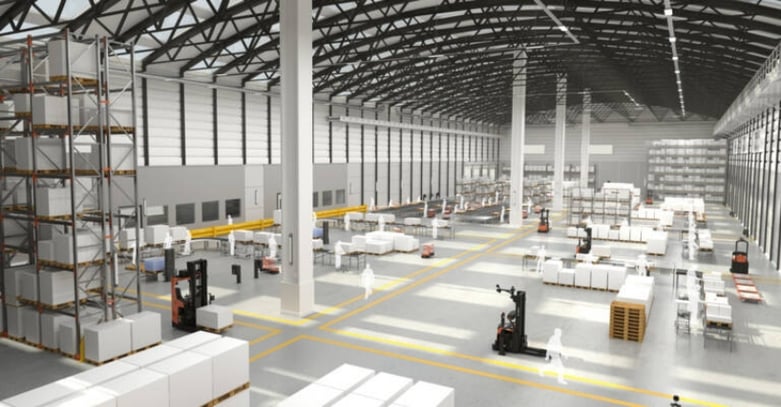
Warehouse automation is designed to automate non-value-added, repetitive processes, freeing up more time for employees to improve decision-making and build a self-sufficient supply chain.
In this resource, we will explore everything there is to know about warehouse automation, including the types of warehouse automation available, the benefits it can offer your business and the importance of optimising your warehouse layout.
- What types of warehouse automation are available?
- What are the benefits of warehouse automation?
- How much does warehouse automation cost?
- What are the challenges of warehouse automation?
- Layout optimisation: What to consider.
- The link between lean production and automation.
- How we helped The Park.
What types of warehouse automation are available?
The number of automated warehouse solutions available to businesses is growing at pace. Different solutions help your business achieve specific goals much quicker. By understanding the different types of warehouse automation available, you can make the most appropriate investment to meet your needs.
Here is a breakdown of the types of warehouse automation available:
Warehouse robotics.
Warehouse robots are automated machines that can move around the warehouse and complete various tasks such as picking, packing, sorting and loading goods. This type of automation is ideal for businesses looking for a cost-effective way to improve productivity in their warehouses.
Automated storage and retrieval systems (AS/RS).
An AS/RS is a computer-controlled system that automates storing and retrieving goods from locations inside the warehouse. These solutions allow for improved accuracy, efficiency and safety when storing and retrieving inventory from your warehouse.
Automated guided vehicles (AGVs).
AGVs provide the physical assets required in a systemic approach to warehouse operations, where common functions — such as material put away or replenishment — can be reworked into configurable modules, with actions delivered by AGVs rather than workers. Essentially, AGVs help to separate repetitive workflows from unique ones.
Automated conveyor systems.
An automated conveyor system moves goods along a series of belts that are powered by motors or other sources of power such as hydraulics or pneumatics. Automated conveyor systems are often used in larger warehouses where goods need to be moved quickly between different locations within the facility.
What are the benefits of warehouse automation?
When utilised effectively, warehouse automation can benefit every area of a business. This section will provide an overview of the key benefits of warehouse automation and why it is worth the investment.
Increased speed and accuracy.
Warehouse automation helps to reduce human error and increase accuracy in order fulfilment. It provides faster processing times, meaning orders can be completed quicker and customer satisfaction is more likely.
Reduced operational costs.
Automation eliminates manual labour costs associated with order picking and sorting processes. Picking errors are an unsurprising occurrence within a warehouse setting. As commonplace as they can be, they should be avoided as each error costs time and profitability. Discover how your business can reduce warehouse picking errors and build a more efficient operation here.
Increased safety and security.
Automation minimises workplace accidents due to reduced human involvement in hazardous processes such as lifting heavy objects and operating machinery. Find out more about examples of warehouse accidents and how to reduce occurrences from happening here.
Reduced human error.
Modern, integrated, intelligent software eliminates human inaccuracies regarding inventory control and management. Deliverable goods will also be processed quickly and with minimum chance of downtime.
Improve sustainability.
Automation can help reduce energy consumption, remove inefficient processes and create more space in your warehouse. It also enables businesses to reduce waste materials and supplies. Find out how here.
How much does warehouse automation cost?
To help you evaluate your decision before investing in warehouse automation solutions, here is an overview of the costs associated and what to consider to take the leap.
What type of costs should you be aware of?
-
Initial Investment: Depending on the level of automation you want to implement, initial investments can reach hundreds of thousands of pounds. Before investing, you should work with a specialist like Toyota Material Handling UK. We will audit your entire warehouse and provide a breakdown of the best solutions for your needs.
-
Labour costs: Although automation will reduce labour costs in the long run, it will usually require highly trained technical staff to maintain and install these systems.
-
Floor space: Be sure to factor in potential floor space costs as part of your considerations. This is why you should always optimise your warehouse layout, which we will discuss later.
What are the challenges of warehouse automation?
Warehouse automation presents a range of challenges your business should address before investing in the solution. By doing so, you can successfully achieve cost savings, improve efficiency and increase customer satisfaction. But what are these challenges and how can you overcome them?
Compliance.
Many industries have regulations that need to be considered when automating business processes. Any changes to the workflow must take the law into account. It is not always easy to do, so we recommend working with an automation specialist like Toyota.
Infrastructure.
Automation requires reliable infrastructure such as power sources, data networks and backup systems. Automated solutions are likely to fail or become unreliable without proper infrastructure in place. You should audit your warehouse before deciding to implement automated solutions.
Training.
Employees must be trained on the new technology for it to be used effectively, but this can be expensive and time-consuming, depending on the complexity of the system being implemented. You also want to ensure the training is worthwhile, which is where an expert like Toyota makes a real difference.
Cost.
Capital is needed to invest in warehouse automation. You need the budget available to make the initial investment and maintain these solutions, which is why you should weigh up your options before jumping into the deep end with warehouse automation. Instead, follow an approach like Kaizen, where continuous improvement is seen over time.
Layout optimisation: What to consider.
A well-designed warehouse layout is a key factor determining a business's productivity and cost-effectiveness. It is also essential that a warehouse is optimally designed to gain a competitive advantage and ensure you are able to make the most of warehouse automation.
There is no one-size-fits-all approach to warehouse layout optimisation, but our seven best practices will aid your redesign efforts.
What are the four best practices for optimising automation and warehouse layout?
-
Identify key areas of improvement:
Start by identifying what areas need improvement within your warehouse operations. This includes picking speed, accuracy of order fulfillment and safety protocols. Once you know what issues need to be addressed, you will have a better idea of what type of automation equipment will help you achieve those goals.
-
Determine appropriate technology:
Once you have identified key areas that need improvement, research different types of automated technologies that might be able to help solve those problems. Consider factors such as cost-effectiveness, ease of use and scalability.
-
Design an efficient layout:
After determining an appropriate technology for each area of improvement identified, it is time to create a plan for how those technologies will fit into your existing warehouse layout—or design a new one if necessary. The three most effective warehouse layouts are:
The L-shaped layout.
The U-shaped layout.
A warehouse may have the loading/unloading space and the shipping space at the tips of the ‘L’. This means the main bulk of the workflow — production and storage — should be housed at the ‘L’ intersection.
The U-shaped layout is a standard design. It features production and storage in the bend of the ‘U’, while loading/unloading and shipping take place in the arms.
The I-shaped layout.
I-shaped layouts denote a warehouse design with loading/unloading at one end of the warehouse and shipping at the other. Production and storage are centrally located. -
Test & document performance:
Once everything is installed properly according to your design plan — it is important to test out every new system before implementing them into daily operations. You should also document performance metrics or KPIs (Key Performance Indicators) to monitor progress over time after any warehouse automation implementation has taken place.
When you are designing the layout of your warehouse, you should keep sustainability in mind. There are a range of initiatives you can implement for sustainable warehouse design, including:
Solar panelled roofs.
Your warehouse should look to reduce its energy consumption — fitting solar panelled roofs on your warehouse can do this. There are three main types of solar panels:
- Monocrystalline solar panels.
- Polycrystalline solar panels.
- Thin-film solar panels.
Decentralised distribution centres.
By strategically positioning your distribution centres, you can limit the sprawl of transporting products and cut back on carbon emissions. Decentralising your distribution centres to smaller warehouses will also allow you to drastically reduce the amount of energy you use and reduce transportation costs.
LED lights and sensors.
Low-energy lights reduce the unnecessary usage of lighting in buildings. They operate using sensors and only turn on if an activity happens in an area. LED lights are also known to have a long lifespan compared to your average incandescent bulb.
Warehouse insulation.
By insulating your warehouse, you can significantly reduce energy bills and greenhouse gas emissions. Having the right insulation in place is also crucial for employee morale. Regulating room temperatures, appropriate sound levels and sustainable methods create a better work atmosphere.
The link between lean production and automation.
Lean production and warehouse automation are both designed to help businesses maximise efficiency while minimising waste.
When it comes to lean production, businesses rely on techniques such as Just-In-Time (JIT) processes and Kanban systems. These aim to streamline operations to reduce wasteful activities and are part if the Toyota Production System (TPS).
By utilising the lean approach in combination with warehouse automation, businesses can optimise operations within the warehouse and the overall supply chain.
The best practices for implementing lean production and warehouse automation together.
There are several best practices that your business can follow to implement lean production effectively in your warehouse. These include:
Establish measurable objectives.
Establishing clear objectives can focus efforts on areas that will yield the most benefit from lean techniques, such as JIT or Kanban systems. You can use these techniques as you start to introduce warehouse automation solutions to your operation. We recommend mapping out SMART objectives. An example of this could be:
Objective: Increase efficiency by 10% in the production process by the end of 2023 by utilising warehouse automation solutions.
Specific: We will increase efficiency by 10% in the production process by December 31, 2023.
Measurable: We will measure our progress in terms of increased efficiency on a monthly basis and how often warehouse automation has contributed to these improvements.
Achievable: We will achieve the 10% efficiency target by implementing warehouse automation solutions such as automated guided vehicles (AGVs).
Relevant: Increasing efficiency in our production process will reduce costs and improve quality, which are important to our customers.
Timely: Our target date to reach the 10% efficiency goal is December 31, 2023.
Start small.
It can be helpful to start with small pilot projects before taking on larger initiatives to gain confidence before making substantial investments. For example, you might invest in one automated truck before you decide that you need a fleet of 50. Again, using the Kaizen methodology of continuous improvement can be beneficial here.
Encourage collaboration.
Involving everyone in the process, from top management down, will help ensure buy-in from all stakeholders. This will make it more likely to see success and fewer challenges when your employees have to embrace change in the workplace. Employees will also be more confident when getting to grips with automated solutions and utilising them for maximum efficiency.
Eliminate non-value-added tasks.
Eliminating non-value-added tasks involves focusing on activities that add value for customers instead of focusing solely on completing tasks that do not provide any tangible value. You should use the 7 wastes of lean manufacturing model to do this. These wastes include:
- Transport: Transportation waste includes the movement of people, tools, inventory, equipment or products.
- Inventory: These include raw materials, supplies and products that are considered a cost to the business until they are sold.
- Motion: The waste in motion includes any unnecessary movement of people, equipment or machinery. Any tasks that require excessive motion should be redesigned to enhance workplace performance.
- Waiting: Waiting for deliverables or lag time between tasks is a waste.
- Overproduction: When a warehouse overproduces the inventory levels needed to meet demand, it is known as overproduction waste.
- Overprocessing: Every warehouse needs processes in place. However, excess processing can harm the entire production chain.
- Defects: Defect waste occurs when a product has flaws once it has made its way through the production process.
How we helped The Park implement warehouse automation solutions.
The Park, a wine distribution business based in the United Kingdom, was looking to streamline their warehouse operations, increase efficiency and overcome the problems associated with the increasingly difficult task of attracting and retaining qualified forklift operators. They turned to Toyota.
After working closely with their team, we provided an integrated warehouse solution tailored to The Park’s individual needs. This included 29 automated reach trucks and a range of manual trucks. By introducing 29 automated reach trucks and a range of manual trucks, they were able to start moving 1.2 million pallets annually and save over £1.6 million each year.
Here is what their General Manager, Richard Lloyd had to say about the project:
“This investment, coupled with others, has given us a phenomenal scale to offer a range of services to other drinks companies with whom we have synergies. By working in partnership with someone that can handle their logistics, packing and warehousing needs, our clients can focus their energy on creating brands. The Park handles every aspect of their fulfilment operation.
More than 40 per cent of all the wine that arrives in Britain is estimated to be brought into the country in bulk tanks before bottling for the simple reason that it is possible to fit close to two and a half times the amount into a shipping container if the wine is stored in a bulk tank rather than bottles.”
You can read the full case study here.
This investment, coupled with others, has given us a phenomenal scale to offer a range of services to other drinks companies with whom we have synergies.Richard Lloyd, The Park General Manager
Speak to us about your needs.
If, like The Park, you are looking to implement automation at your business, we would love to support you on your journey. We ensure you get the most out of your equipment and warehouse configuration — from the shop floor to the site infrastructure.
It all starts with a conversation. Our team of experts will get to know your business, goals and the current landscape of your operation. From there, we will work together to map out potential solutions that can help you go in one direction — the right one.
Are you ready to get started on your warehouse automation journey? Click below.