Optimising warehouse performance through effective supply chain management.
Supply chain management refers to coordinating and controlling various activities and processes involved in moving and storing goods within a warehouse facility.
However, managing the intricacies of supply chain management can pose a significant challenge, given its multifaceted nature and the numerous variables involved in the process.
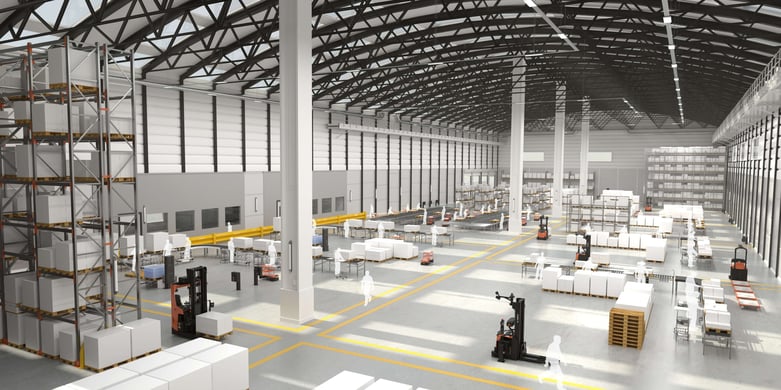
Staying ahead and maintaining control requires careful attention and proactive measures.
This page explains the key elements of effective supply chain management and offers helpful resources to further your understanding.
Throughout the page, we will cover the following sections. Click any of the following headings or the contents tab to the left to take you to the relevant section.
The importance of a well-managed supply chain.
Efficient supply chain management is crucial for the success of any warehouse operation. Streamlining processes, optimising resources and ensuring the timely delivery of goods can significantly impact a warehouse's overall performance and profitability.
While effective supply chain management offers numerous benefits — as outlined in this blog — it also poses several challenges.
Warehouses must navigate complexities such as demand volatility, fluctuating market conditions, global supply chain disruptions and rising customer expectations.
Despite the challenges, supply chain management in warehouses presents opportunities for improvement and growth. By embracing technological advancements, adopting sustainable practices and implementing data-driven decision-making processes, warehouses can gain a competitive edge.
We’ll show you exactly how to do that on this page.
Benefits of well-managed inventory and how to achieve them.
Inventory management encompasses various practices and strategies to efficiently handle and control the inventory or stock of goods within a warehouse setting.
By implementing effective inventory management techniques, businesses can ensure they are well-prepared to handle fluctuations in customer demand, ultimately leading to improved customer satisfaction and a competitive edge in the market.
The benefits of well-managed inventory.
One of the primary benefits of inventory management is its ability to help businesses cope with changes in demand. Customer demand is only sometimes predictable and can fluctuate due to seasonal trends, market conditions or unexpected events.
By maintaining a well-managed inventory, warehouse operators can promptly adjust stock levels to meet customer requirements. This prevents situations where goods are out of stock or excess inventory accumulates, leading to missed sales opportunities or unnecessary carrying costs.
Other benefits of well-managed inventory include:
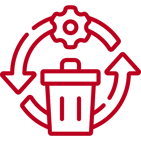
Minimised risk of waste.
Key strategies for optimising warehouse inventory management.
To reap these benefits, implementing strategic inventory management techniques is an excellent place to start. Here are three strategies you can implement in your warehouse:
1. Optimise the layout of your warehouse.
The layout of a warehouse directly impacts the efficiency of goods control and the overall flow of operations within the facility. As the supply and demand of products tend to change seasonally, it is important to regularly review and update the warehouse layout to proactively address these fluctuations.
2. Implement warehouse automation.
Implementing automated solutions, such as dedicated warehouse robotics, can alleviate much of the burden placed on the workforce. These advanced technologies take on labour-intensive tasks, providing enhanced visibility and clarity regarding the location of products and materials within the supply chain.
3. Label your inventory.
Implementing clear rack labels, bin labels and warehouse signage has multiple benefits, including streamlined processes, reduced picking errors and improved navigation for your staff, particularly during busier periods.
Visit our blog linked below for a more in-depth look into these strategies, plus discover two more strategies that will help you optimise your warehouse inventory management, including other helpful resources.
Warehouse layout and design: Best practices for optimisation.
Warehouse layout design is a vital component of supply chain management as it directly influences the efficiency and effectiveness of warehouse operations.
A well-designed layout maximises storage capacity and throughput by optimising space utilisation while minimising costs.
It streamlines workflow, ensuring smooth processes from receiving to shipping, reducing bottlenecks and improving productivity.
The design also enhances inventory management by facilitating organised storage, easy access and accurate order picking.
However, designing a well-functioning warehouse layout is challenging due to the complex nature of warehouse operations and no one-size-fits-all approach exists.
So, follow these best practices to give you a head start on optimising your warehouse layout and design.
Best practices for warehouse layout optimisation.
- Mapping your warehouse — Create a precise blueprint of your warehouse. Once the warehouse mapping is completed, you can begin redesigning to achieve optimisation.
- Choose your storage areas — Determine the size of your storage areas. To do this, you need to multiply the square footage of your racking by the height of the highest potential load that the storage area can accommodate. This calculation will give you the size of the possible storage area. For an example of how to do this calculation, read this blog.
- Designate storage space for specific products — Optimise the allocation of storage space based on the specific characteristics of the products. For instance, small products should be placed in appropriately sized spaces, as storing them in larger spaces would result in inefficient space utilisation. Matching the storage space's size to the products' dimensions and quantity ensures efficient space management and prevents wastage.
These practices are an excellent start, but familiarise yourself with four other crucial practices that will complete all you need to know about optimising your warehouse layout and design. You can find them in the blog linked below.
Transportation management: How to optimise shipping and receiving.
Transportation management is a crucial link between suppliers, manufacturers, distributors and customers. It involves the planning, execution and control of the movement of goods from one location to another — in other words, shipping and receiving.
By aligning transportation decisions with broader supply chain strategies, warehouses can enhance operational efficiency and improve customer satisfaction.In this section, we’ll explore the key components of transportation management and provide valuable guidance on optimising transportation management for a seamless supply chain operation.
Carrier selection — choosing the right partners.
Selecting the right carriers is essential to ensure reliable and cost-effective transportation. Factors such as carrier reputation, service quality, coverage area, capacity and pricing should be carefully considered. Collaborating with reputable carriers who align with your business requirements can significantly impact the overall supply chain performance.
Routing — efficient movement of goods.
Proper routing involves determining the most efficient paths for transporting goods. Factors like distance, traffic conditions, delivery deadlines and mode of transportation should be considered. Optimised routing saves time and fuel costs and enhances overall supply chain efficiency.
Tracking — real-time visibility of shipments.
Real-time tracking enables warehouse managers to monitor the movement of goods throughout transportation. Utilising advanced tracking technologies, such as GPS and RFID, provides accurate location information, improves security and allows proactive management of potential delays or disruptions.
Optimisation through technology and data analytics.
Technology and data analytics have revolutionised transportation management in supply chain operations. Leveraging transportation management systems (TMS) and advanced analytics tools helps optimise various aspects of the transportation process.
Predictive analytics can identify trends, anticipate bottlenecks and suggest efficient routes, ultimately improving overall transportation efficiency.
Discover the power of automation and technology.
In an era where speed and accuracy are paramount, warehouse automation has emerged as a vital component in supply chain management.
By harnessing the power of technology, businesses can automate various tasks and processes within a warehouse, leading to improved operational efficiency, cost savings and better customer experiences.
The need for warehouse automation arises from the ever-increasing customer demands, global supply chain complexities and the drive for operational excellence.
Manual processes and traditional warehousing methods often fail to meet these challenges efficiently.
By leveraging technology, businesses can overcome these limitations and achieve:
Enhanced efficiency and productivty.
Cost savings and return of investment.
Improved accuracy and reduced errors.
Optimised space utilisation.
Types of automation machinery available.
Companies face immense pressure to stay ahead and meet the ever-increasing demands of customers. One crucial aspect that plays a significant role in maintaining a competitive edge is the speed and accuracy of manufacturing and distribution processes.
This is where automated machinery emerges as a vital solution. Let’s discover the type of automation machinery available and how they can be used within warehouses.
- Automated guided vehicles (AGVs) — Designed to navigate and transport materials or goods within a controlled environment without the need for human intervention due to advanced technology and sensors that allow them to operate autonomously or under minimal supervision.
- Goods-to-person (G2P) automation — Items or goods are brought to the operator or worker rather than the worker physically moving to retrieve the items. It involves using automated technologies and systems to streamline the order fulfilment process and increase operational efficiency.
- Collaborative robots — A type of robot, also known as cobots, designed to work alongside humans in a shared workspace or environment. Unlike traditional industrial robots that typically operate in separate, isolated areas, cobots are intended to collaborate directly with human workers, assisting them in various tasks.
The use of automation in warehouses is not only essential but also fascinating. To learn more about the different types of automation machinery and how they can apply to warehouses, visit our blog below.
Analyse your supply chain and start optimising today.
As a warehouse manager, you should regularly analyse your supply chain and introduce new initiatives to optimise your operation.
This will allow you to identify inefficiencies, bottlenecks and areas for improvement, ultimately leading to increased productivity, reduced costs and improved customer satisfaction.
By analysing your supply chain, you can identify areas of waste, streamline processes and implement innovative solutions such as automation or improved inventory management, ultimately resulting in a more efficient and competitive warehouse operation.
To further assist you with this, you can download our supply chain profitability playbook that explains the most impactful strategies to improve your supply chain, generate more revenue and continue growing your business.
Have it sent directly to your inbox by clicking on the link below.