Lean production for logistics managers.
In today’s challenging business environment, logistics managers face increasing pressure to generate efficiencies, enhance customer satisfaction and reduce costs.
One way to achieve these goals and develop a better workplace is the implementation of lean production principles.
.jpg?width=781&height=521&name=production-mjolby-factory-8%20(5).jpg)
Lean production is a philosophy that seeks to reduce waste and improve efficiency across the production process.
This page will outline the benefits and best practices for implementing lean thinking across your business, focusing on its contribution towards efficiency and sustainability.
Throughout the page, we will cover the following sections. Click any of the following headings or the contents tab to the left to take you to the relevant section.
An overview of lean production, its principles and benefits.
Lean production is a system of manufacturing or managing operations that focuses on maximising efficiency, improving quality and reducing waste.
The approach originated in Japan in the 1940s and 1950s with the Toyota Production System (TPS). It has since spread globally and is widely used in various industries.
Also referred to as lean thinking, lean production aims to optimise the use of resources, reduce unnecessary inventory and maximise productivity. Its goal is to ensure products move through the supply chain as quickly and efficiently as possible, reducing lead times.
Lean production also ties in with your overall sustainability strategy. Minimising waste and using resources can result in significant environmental benefits, such as reduced greenhouse gas (GHG) emissions and the conservation of natural resources.
Keeping lean principles in mind, you can assess your resource usage and waste across your processes, fine-tuning your operations to aid the environment.
Lean thinking is more of a philosophy than a practice and there are five principles you must follow to maximise its effectiveness.
The five principles of lean.
A lean thinking approach can help your business improve flow in the value stream, reduce waste and become more sustainable.
If your business is looking to become leaner in its approach, there are five key principles of lean thinking to learn.
- Defining value.
- Mapping value streams.
- Creating flow.
- Establishing pull.
- Seeking perfection.
Reaping the benefits of lean production starts with a shift in mindset. Learn about these five principles in detail by exploring our blog post.
Information and guidance on implementing lean production in your business.
Implementing lean production in your business involves a series of strategic steps to ensure success. One popular framework is the 5S framework, a methodology that results in a clean and safe workplace, reducing waste and optimising productivity.
The 5S framework is broken down into the following:
- Step one: Sort.
- Step two: Set.
- Step three: Shine.
- Step four: Standardise.
- Step five: Sustain.
If you want to implement lean production within your business, then the 5S framework is a great approach.
Head to our blog post to learn more about what is involved in the five steps.
A crucial part of implementation is identifying areas for improvement — you will focus on increasing productivity and reducing waste in these areas. To ensure success across your identified areas, you must create a lean team to oversee the implementation process.
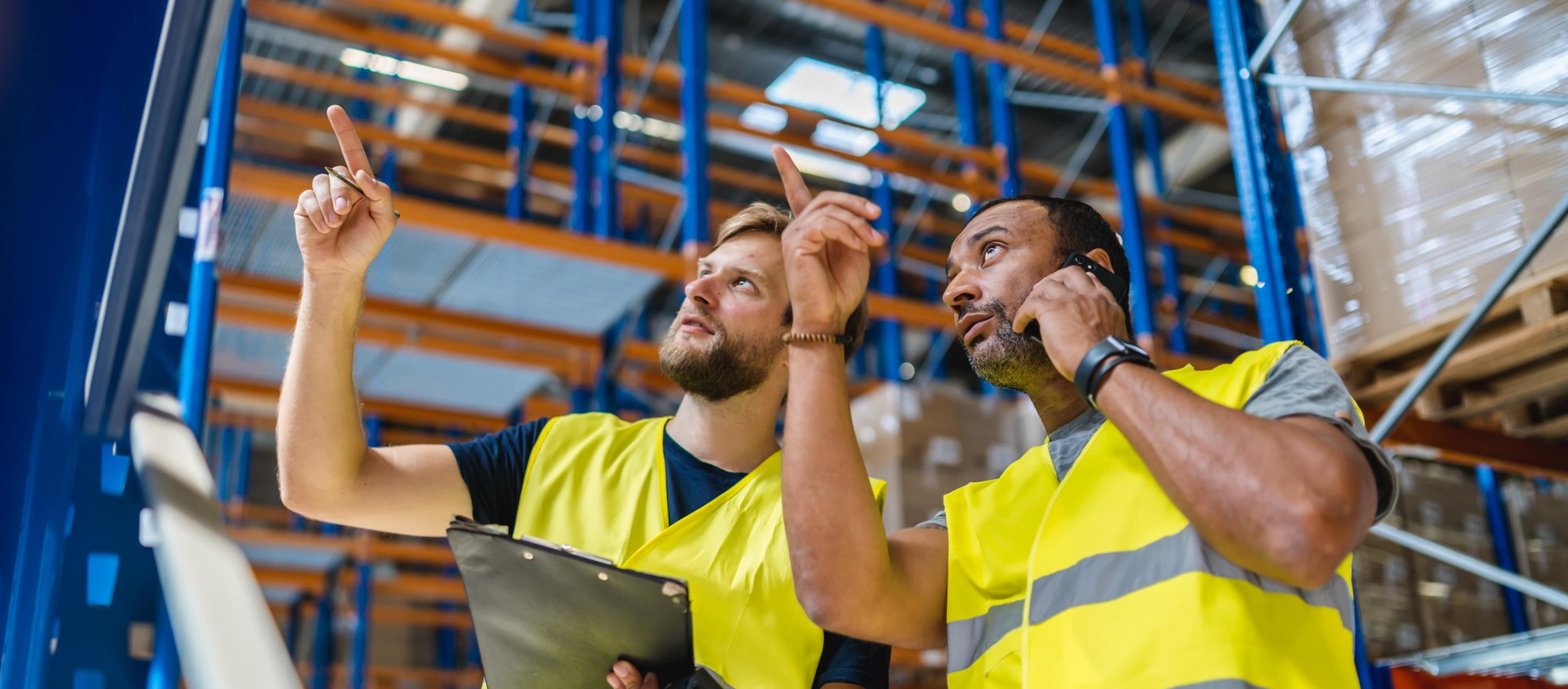
Your team should have staff members with various skills and experience, including logistics managers, process improvement specialists and warehouse operators. The lean team will work together to develop the plan that targets these improvement areas, setting goals and timelines for achieving them.
It is vital to involve logistics managers throughout the implementation process due to their knowledge of moving goods within the business. They can provide valuable insights into your current processes, allowing you to pinpoint those improvement areas easily.
Lean production: Best practices, benefits and challenges.
By following lean production best practices, you can streamline your processes and generate efficiencies across your business.
These methods include creating standardised processes, reducing waste, improving communication and continuously monitoring performance.
Successful implementation can lead to several benefits, including:
- Improved performance.
- Better inventory management.
- Improved lead times.
- Increased profitability.
- A happier workforce.
These are just five of the nine benefits we explore in our blog post. Learn more about the benefits of lean production in detail by clicking below.
As with all process adjustments, there will be challenges to overcome. These can include:
Overcoming these challenges requires effective communication, a commitment to your targeted improvements and strong leadership.
However, the benefits outweigh the cons if you strategically implement lead production in your business. Visit our lean principles benefits blog post to understand what you can expect from a successful implementation.
The tools and techniques used in lean production.
One of the core principles of lean production is reducing waste; waste is defined as activities that do not add value to the product or service.
Logistics managers can implement several tools and techniques to meet this core principle. These include:
- Kaizen.
- The 5S methodology.
- Value stream mapping (VSM).
- The six big losses.
- Bottleneck analysis.
The Kaizen methodology focuses on continuous improvement, which is a process that involves identifying and eliminating waste through structured problem-solving and experimentation.
It empowers individuals to identify areas for improvement and suggest practical solutions, humanising the workforce and raising employee morale in the process.
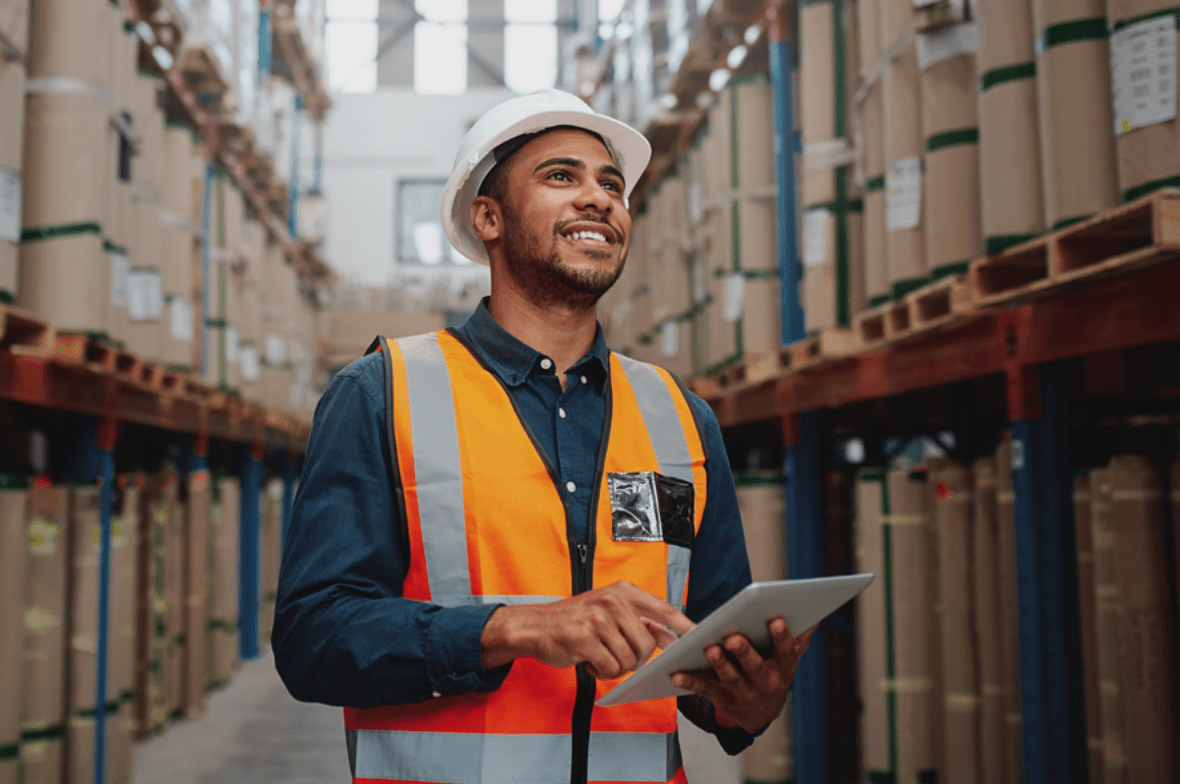
Alongside techniques like the Kaizen methodology, logistics managers can use lean management tools, such as VSM.
VSM allows businesses to visualise the steps needed to optimise value throughout the supply chain. It reviews the flow of steps and information from origin to delivery, allowing companies to detect and mitigate waste areas.
If you want to learn more about the best tools and techniques for lean production, head to our blog post exploring each of the five methods listed above.
The seven wastes of lean manufacturing.
When establishing your company’s types of waste, you can refer to the ‘seven wastes of lean manufacturing’ concept.
This concept dates back to the middle of the 20th century and is a core principle of the Toyota Production System (TPS). The seven types of waste in lean manufacturing are:
- Transport. The movement of people, tools, inventory, equipment or products.
- Inventory. Having more inventory than necessary can lead to a combination of waste build-up.
- Motion. The unnecessary movement of people, equipment or machinery, or tasks that require excessive motion.
- Waiting. This type of waste can occur when the production line stands still, as your staff cannot complete their jobs.
- Overproduction. When a warehouse overproduces the required inventory levels needed to meet demand.
- Overprocessing. All warehouses need processes, but excess processing can do more harm than good.
- Defects. Occurs when products are found to have flaws once they have made their way through production.
If your business suffers from any of the seven wastes of lean manufacturing, our blog post can help. It thoroughly explores the seven wastes and offers solutions to remedy your problems.
An overview of lean automation's benefits.
Businesses have several goals to meet — reducing waste, maximising productivity and generating efficiencies, to name a few.
Lean automation sees the implementation of automated solutions across the supply chain, helping make processes more efficient and less error-prone.
Other benefits of lean automation include the following:
- Optimised production processes.
- Reduced need for human intervention.
- Reduced operational costs.
- Optimised assembly line.
- Improved product quality.
Automation software is one of the most prevalent solutions available and can take over manual tasks like asset management and stock-taking.
For example, automated guided vehicles (AGVs) help businesses streamline their processes and reduce errors in the production cycle. These vehicles can range from tow trains to shuttles and carts. You can learn more about these vehicles and the benefits they provide here.
Implementing lean automation comes with its challenges. One of the biggest hurdles is the initial investment in technology and maintaining it after its implementation.
Another difficulty is the integration of technology into existing processes. With lean automation, there needs to be a company-wide buy-in to ensure you extract the maximum potential from your technology.
Despite implementation challenges, lean automation can bring several benefits to logistics managers, including improved productivity and reduced time for task completion.
.jpeg?width=2000&height=1000&name=toyotafactoryrender%20(1).jpeg)
Logistics managers can expect the following benefits from the successful implementation of lean automation:
Increased worker safety.
Reduced lead times.
Improved accuracy.
Reduced
costs.
By following four simple steps — Plan, Do, Check and Act — logistics managers can identify opportunities to implement lean automation across the supply chain.
To learn more about these four steps and how they can help you implement lean automation, read our blog post by clicking below.
The connection between lean production and sustainability.
Lean thinking considers the waste generated from uneven workloads and redundant processes and what can be done to maximise efficiency and decrease costs in these areas.
With more efficient processes comes a more sustainable way of working if appropriately managed. Sustainable supply chains aim to minimise negative environmental, economic and social impacts while ensuring long-term viability.
The practical steps for building a sustainable supply chain include:
- Identify sustainability issues in the supply chain. This step involves an audit and analysis of your entire supply chain, allowing you to identify elements that can be made more sustainable. You can use lean production techniques to support you with your analysis, including value stream mapping (VSM).
- Adopt a circular supply chain. Eliminating waste should be a top priority. To do this, adopting a circular supply chain is recommended. A circular supply chain can be achieved by recycling the raw materials you use and reintroducing them into your manufacturing operation.
- Work with sustainable suppliers. You can control most of your supply chain, but your suppliers will have some influence. This is why it is essential to partner with suppliers that demonstrate a commitment to sustainability, even it if means changing from suppliers you have worked with for some time.
- Drive continuous improvement. A sustainable supply chain can only be achieved if your business fully commits to the cause. You can accomplish this in several ways — visit our blog below to learn more.
%20(1)-1.png)
So, how do lean principles contribute to a more sustainable organisation? There are three main schools of thought:
- Start reducing waste.
- Use fewer resources.
- Eliminate redundant processes.
Waste can be defined as anything that does not add value to the production process, and seven different types of waste are generated in businesses. You can read about these seven different types here.
Using fewer resources goes hand-in-hand with a reduction of waste. Not utilising resources efficiently, such as energy, materials and transport, can cause damage to your business and the environment.
You will also want to eliminate any unnecessary processes from your supply chain. Overprocessing is referred to as the unnecessary addition of more components or steps to a process than what is required.
There are several lean techniques your business can leverage to identify and eliminate redundant processes and begin to run a more efficient operation, becoming more sustainable as a result.
Read about these methods by visiting our blog post on how lean principles can lead to a more sustainable way of working.
How lean production can improve warehouse efficiency.
Warehouse efficiency is critical to business success for companies that rely on inventory management. Inefficient warehouse operations can lead to high storage costs, poor customer service and long lead times.
Implementing lean production can result in several efficiencies for your business. If you are looking to improve both the efficiency and the sustainability of your warehouse, there are several ideas you can implement to do so.
To get you started, here are 11 ways you can look to improve warehouse efficiency:
- Install eco lighting.
- Integrate renewable energy solutions.
- Invest in insulation.
- Look to lean principles.
- Adopt automation.
- Reduce water waste.
- Pick sustainable packaging.
- Optimise waste management.
- Start a ‘reuse’ programme.
- Opt for efficient equipment.
- Revise warehouse layout.
Our blog post explores these 11 impactful strategies in detail and provides a resource that will give you the confidence to implement them.
Identifying whether your business suffers from common inefficiencies and addressing these areas is also essential.
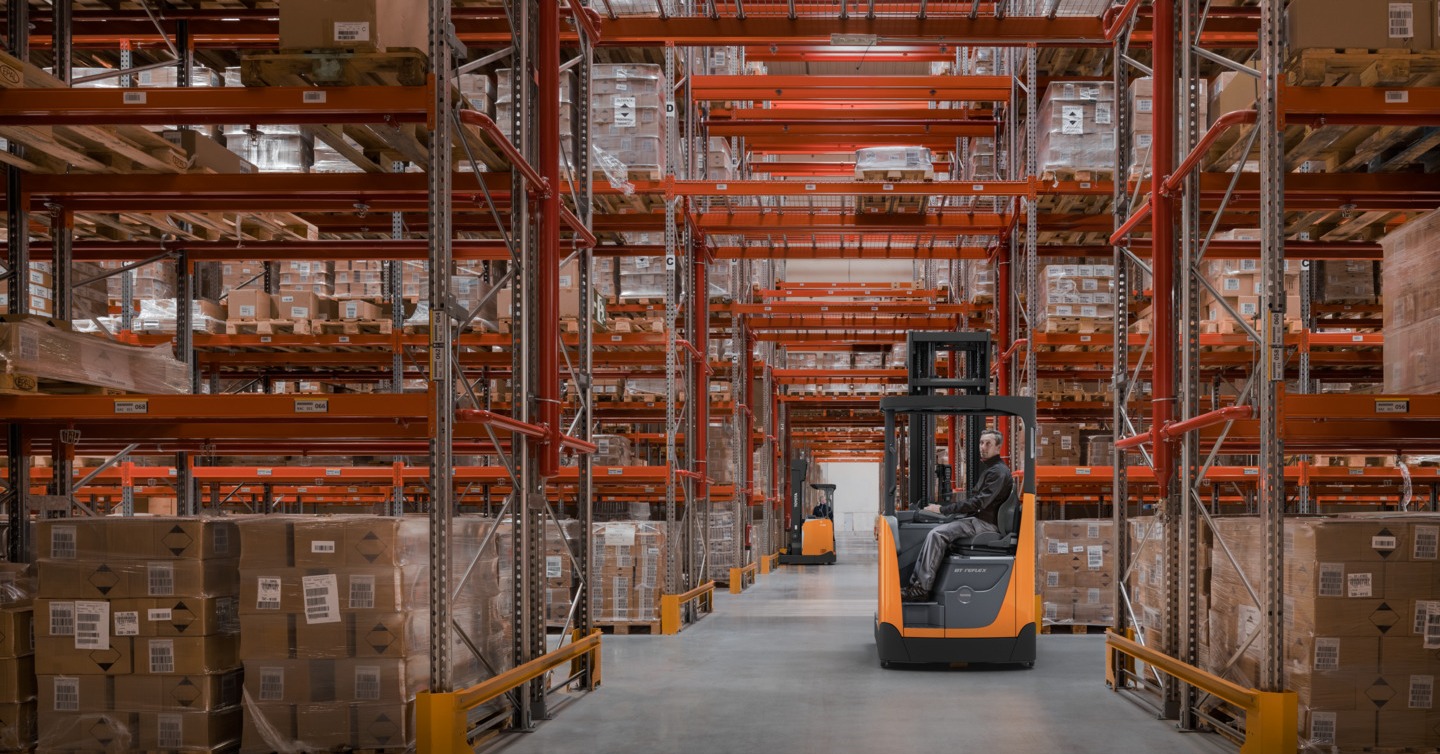
For example, a poorly designed warehouse layout can lead to the breakdown of processes, and poor inventory management can lead to inefficiencies in managing supply and demand.
Your business should always look to implement continuous improvement. This can be done by consistently revising processes and introducing new technology.
Plus, by adopting a methodology such as Kaizen, you can work closely with your employees to understand how your business should operate.
There are five common inefficiencies you should look out for in your business. Our blog post explores these five inefficiencies and what you can do to optimise them.
Start implementing lean production today.
By adopting lean thinking, your business can generate several efficiencies and become more sustainable and profitable — all while creating a happier workforce.
Within lean thinking and lean production, there are many things to consider. Awareness of the industry’s best methodologies can reduce waste and improve processes.
If you want to bake lean production into your processes, the following resource provides several strategies for doing so.
It walks you through the core principles of lean production and how it can improve operational efficiency.
To download your free copy of the guide, click below.